Dentro del campo de la soldadura industrial, la soldadura eléctrica manual al arco con electrodo revestido es la más utilizada. Para ello se emplean máquinas eléctricas de soldadura que básicamente consisten en transformadores que permiten modificar la corriente de la red de distribución, en una corriente tanto alterna como continua de tensión más baja, ajustando la intensidad necesaria según las características del trabajo a efectuar.
Los trabajos con este tipo de soldadura conllevan una serie de riesgos entre los que destacan los relacionados con el uso de la corriente eléctrica, los contactos eléctricos directos e indirectos y otros; el objetivo es dar a conocer las características técnicas básicas de la soldadura eléctrica, los riesgos y sus factores de riesgo y los sistemas de prevención y protección. Además, se dan normas de seguridad para la organización segura del puesto de trabajo, los equipos de protección individual y el mantenimiento e inspección del material.
Características técnicas
- Arco eléctrico
Para unir dos metales de igual o parecida naturaleza mediante soldadura eléctrica al arco es necesario calor y material de aporte (electrodos). El calor se obtiene mediante el mantenimiento de un arco eléctrico entre el electrodo y la pieza a soldar (masa) (fig. 1). En este arco eléctrico a cada valor de la intensidad de corriente, corresponde una determinada tensión en función de su longitud. La relación intensidad/tensión nos da la característica del arco. Para el encendido se necesita una tensión comprendida entre 40 y 110 V; esta tensión va descendiendo hasta valores de mantenimiento comprendidos entre 15 y 35 V, mientras que la intensidad de corriente aumenta notablemente, presentando todo el sistema una característica descendente, lo que unido a la limitación de la intensidad de corriente cuando el arco se ha cebado exige, para el perfecto control de ambas variables, la utilización de las máquinas eléctricas de soldadura.
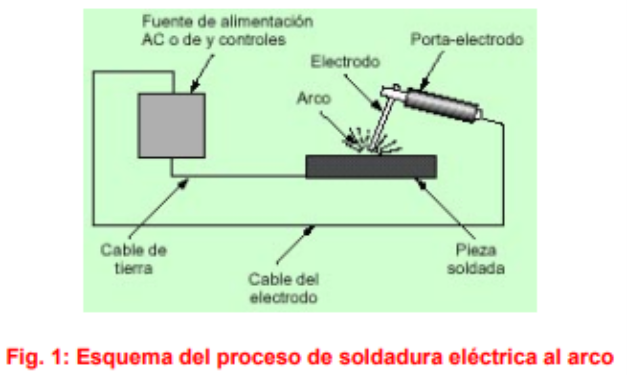
- Equipos eléctricos de soldar
Están formadas por el circuito de alimentación y el equipo propiamente dicho. Sirven para reducir la tensión de red (220 o 380 V) a la tensión de cebado (entre 40 y 100 V) y de soldeo (< 35 V) permitiendo regular la intensidad de la corriente de soldadura, asegurando el paso de la tensión de cebado a la de soldeo de forma rápida y automática. El circuito de alimentación está compuesto por un cable y clavija de conexión a la red y funcionando a la tensión de 220/380 V según los casos e intensidad variable.
- Equipo de soldadura
En función del tipo de corriente del circuito de soldeo el equipo consta de partes diferentes. En equipos de corriente alterna, – transformador y convertidor de frecuencia; en equipos de corriente continua, rectificador (de lámparas o seco) y convertidor (conmutatrices o grupos eléctricos). Los equipos eléctricos de soldar más importantes son los convertidores de corriente alterna-continua y corriente continua-continua, los transformadores de corriente alterna-corriente alterna, los rectificadores y los transformadores convertidores de frecuencia. Además de tales elementos existen los cables de pinza y masa, el porta electrodos y la pinza-masa, a una tensión de 40 a 100 V, que constituyen el circuito de soldeo.
- Elementos auxiliares
Los principales son los electrodos, la pinza porta electrodos, la pinza de masa y los útiles. El electrodo es una varilla con un alma de carbón, hierro o metal de base para soldeo y de un revestimiento que lo rodea. Forma uno de los polos del arco que engendra el calor de fusión y que en el caso de ser metálico suministra asimismo el material de aporte.
Existen diversos tipos, pero los más utilizados son los electrodos de revestimiento grueso o recubiertos en los que la relación entre el diámetro exterior del revestimiento y el del alma es superior a 1:3. El revestimiento está compuesto por diversos productos como pueden ser: óxidos de hierro o manganeso, ferromanganeso, rutilo, etc.; como aglutinantes se suelen utilizar silicatos alcalinos solubles. La pinza porta electrodos sirve para fijar el electrodo al cable de conducción de la corriente de soldeo.
La pinza de masa se utiliza para sujetar el cable de masa a la pieza a soldar facilitando un buen contacto entre ambos. Entre los útiles, además de los martillos, tenazas, escoplos, etc. el soldador utiliza cepillos de alambre de acero para limpieza de superficies y martillos de punta para romper la cubierta de las escorias o residuos.
Riesgos y factores de riesgo
- Riesgos de accidente
Los principales riesgos de accidente son los derivados del empleo de la corriente eléctrica, las quemaduras y el incendio y explosión. El contacto eléctrico directo puede producirse en el circuito de alimentación por deficiencias de aislamiento en los cables flexibles o las conexiones a la red o a la máquina y en el circuito de soldadura cuando está en vacío (tensión superior a 50 V).
El contacto eléctrico indirecto puede producirse con la carcasa de la máquina por algún defecto de tensión. Las proyecciones en ojos y las quemaduras pueden tener lugar por proyecciones de partículas debidas al propio arco eléctrico y las piezas que se están soldando o al realizar operaciones de descascarillado.
La explosión e incendio puede originarse por trabajar en ambientes inflamables o en el interior de recipientes que hayan contenido líquidos inflamables o bien al soldar recipientes que hayan contenido productos inflamables.
- Riesgos higiénicos
Básicamente son tres: la exposición a radiaciones ultravioleta y luminosas, la exposición a humos y gases y la intoxicación por fosgeno. Las exposiciones a radiaciones ultravioleta y luminosas son producidas por el arco eléctrico.
La inhalación de humos y gases tóxicos producidos por el arco eléctrico es muy variable en función del tipo de revestimiento del electrodo o gas protector y de los materiales base y de aporte y puede consistir en exposición a humos (óxidos de hierro, cromo, manganeso, cobre, etc.) y gases (óxidos de carbono, de nitrógeno, etc).
Finalmente, puede ocurrir intoxicación por fosgeno cuando se efectúan trabajos de soldadura en las proximidades de cubas de desengrase con productos clorados o sobre piezas húmedas con dichos productos.
Sistemas de prevención y protección
- Contactos eléctricos directos e indirectos
Equipo de soldar
La máquina de soldar puede protegerse mediante dos sistemas, uno electromecánico que consiste en introducir una resistencia en el primario del transformador de soldadura (resistencia de absorción) para limitar la tensión en el secundario cuando está en vacío y otro electrónico que se basa en limitar la tensión de vacío del secundario del transformador introduciendo un TRIAC en el circuito primario del grupo de soldadura. En ambos casos se consigue una tensión de vacío del grupo de 24 V, considerada tensión de seguridad.
Pinza porta electrodos
La pinza debe ser la adecuada al tipo de electrodo utilizado y que además sujete fuertemente los electrodos. Por otro lado, debe estar bien equilibrada por su cable y fijada al mismo de modo que mantenga un buen contacto. Asi mismo el aislamiento del cable no se debe estropear en el punto de empalme.
Circuito de acometida
Los cables de alimentación deben ser de la sección adecuada para no dar lugar a sobrecalentamientos. Su aislamiento será suficiente para una tensión nominal > 1000 V. Los bornes de conexión de la máquina y la clavija de enchufe deben estar aislados.
Circuito de soldadura
Los cables del circuito de soldadura al ser más largos deben protegerse contra proyecciones incandescentes, grasas, aceites, etc., para evitar arcos o circuitos irregulares.
Carcasa
La carcasa debe conectarse a una toma de tierra asociada a un interruptor diferencial que corte la corriente de alimentación en caso de que se produzca una corriente de defecto.
Radiaciones ultravioletas y luminosas
Se deben utilizar mamparas de separación de puestos de trabajo para proteger al resto de operarios. El material debe estar hecho de un material opaco o translúcido robusto. La parte inferior debe estar al menos a 50 cm del suelo para facilitar la ventilación. Se debería señalizar con las palabras: PELIGRO ZONA DE SOLDADURA, para advertir al resto de los trabajadores.
El soldador debe utilizar una pantalla facial con certificación de calidad para este tipo de soldadura, utilizando el visor de cristal inactínico cuyas características varían en función de la intensidad de corriente empleada. Para cada caso se utilizará un tipo de pantalla, filtros y placas filtrantes que deben reunir una serie de características función de la intensidad de soldeo y que se recogen en tres tablas; en una primera tabla se indican los valores y tolerancias de transmisión de los distintos tipos de filtros y placas filtrantes de protección ocular frente a la luz de intensidad elevada.
Por otro lado, para elegir el filtro adecuado (Nº de escala) en función del grado de protección se utiliza otra tabla que relaciona los procedimientos de soldadura o técnicas relacionadas con la intensidad de corriente en amperios.
Proyecciones y quemaduras
Se deben emplear mamparas metálicas de separación de puestos de trabajo para que las proyecciones no afecten a otros operarios. El soldador debe utilizar pantalla de protección. El filtro de cristal inactínico debe ser protegido mediante la colocación en su parte anterior de un cristal blanco.
Exposición a humos y gases
Se debe instalar un sistema de extracción localizada por aspiración que capta los vapores y gases en su origen con dos precauciones: en primer lugar, instalar las aberturas de extracción lo más cerca posible del lugar de soldadura; en segundo, evacuar el aire contaminado hacia zonas donde no pueda contaminar el aire limpio que entra en la zona de operación. Describimos cuatro formas de instalar sistemas de extracción localizada.
La campana móvil es un sistema de aspiración mediante conductos flexibles. Hace circular el aire sobre la zona de soldadura a una velocidad de al menos 0,5 m/s. Es muy importante situar el conducto lo más cerca posible de la zona de trabajo.
La mesa con aspiración descendente consiste en una mesa con una parrilla en la parte superior. El aire es aspirado hacia abajo a través de la parrilla hacia el conducto de evacuación. La velocidad del aire debe ser suficiente para que los vapores y los gases no contaminen el aire respirado. Las piezas no deben ser demasiado grandes para no cubrir completamente el conducto e impedir el efecto de extracción.
Un recinto acotado consiste en una estructura con techo y dos lados que acotan el lugar donde se ejecutan las operaciones de soldadura. El aire fresco llega constantemente al recinto. Este sistema hace circular el aire a una velocidad mínima de 0,5 m/s.
Los conductos de extracción constan de una entrada de gas inerte que circula por un tubo hacia la zona de soldadura y luego junto con los vapores y gases es conducido por un tubo de salida hacia la cámara de extracción y después al sistema de evacuación.
Cuando la soldadura se efectúe en recintos cerrados de pequeñas dimensiones y sin ventilación, el soldador deberá estar equipado con un equipo autónomo o con suministro de aire desde el exterior que además cumplirá con la protección contra las radiaciones.
Intoxicación por fosgeno
No se deben realizar operaciones de soldadura en las proximidades de cubas de desengrase con productos clorados o sobre piezas húmedas.
Normas de seguridad
- Puesta a tierra
La instalación de las tomas de la puesta a tierra se debe hacer según las instrucciones del fabricante. Es preciso asegurarse de que el chasis del puesto de trabajo está puesto a tierra controlando en especial las tomas de tierra y no utilizar para las tomas de la puesta a tierra conductos de gas, líquidos inflamables o eléctricos.
La toma de corriente y el casquillo que sirve para unir el puesto de soldadura a la fuente de alimentación deben estar limpios y exentos de humedad. Antes de conectar la toma al casquillo se debe cortar la corriente. Una vez conectada se debe permanecer alejado de la misma. Cuando no se trabaje se deben cubrir con capuchones la toma y el casquillo.
- Conexiones y cables
Se debe instalar el interruptor principal cerca del puesto de soldadura para en caso necesario poder cortar la corriente. Instalar los- principales cables de alimentación en alto y conectarlos posteriormente.
Desenrollar el cable del electrodo antes de utilizarlo, verificando los cables de soldadura para comprobar que su aislamiento no ha sido dañado y los cables conductores para descubrir algún hilo desnudo. Verificar asimismo los cables de soldadura en toda su longitud para comprobar su aislamiento, comprobando que el diámetro del cable de soldadura es suficiente para soportar la corriente necesaria. Hay que tener en cuenta que a medida que la longitud total del cable aumenta, disminuye su capacidad de transporte de corriente. Por tanto, para según qué casos se deberá aumentar el grosor del cable.
Se debe reemplazar cualquier cable de soldadura que presente algún tipo de ligadura a menos de 3 m del porta electrodos. No utilizar tornillos para fijar conductores trenzados pues acaban por desapretarse.
Montaje correcto del puesto de trabajo
- Recomendaciones
Se deben alejar los hilos de soldadura de los cables eléctricos principales para prevenir el contacto accidental con el de alta tensión, así como cubrir los bornes para evitar un posible cortocircuito causado por un objeto metálico y situar el material de forma que no sea accesible a personas no autorizadas.
Las tomas de corriente deben situarse en lugares que permitan su desconexión rápida en caso de emergencia y comprobar que el puesto de trabajo está puesto a tierra.
El puesto de soldadura debe protegerse de la exposición a gases corrosivos, partículas incandescentes provocadas por la soldadura o del exceso de polvo; el área de trabajo debe estar libre de materias combustibles. Si algún objeto combustible no puede ser desplazado, debe cubrirse con material ignífugo. Debe disponerse de un extintor apropiado en las proximidades de la zona de trabajo.
- Prohibiciones
No se deben bloquear los pasillos. Los conductores deben estar situados en alto o recubiertos para no tropezar con ellos. Los cables y conductores no deben obstruir los pasillos, escaleras u otras zonas de paso. El puesto de soldadura no debe situarse cerca de puentes-grúa o sobre los pasillos.
La toma de tierra no debe unirse a cadenas, cables de un montacargas o tornos. Tampoco se debe unir a tuberías de gas, líquidos inflamables o conducciones que contengan cables eléctricos.
Se debe evitar que el puesto de soldadura esté sobre zonas húmedas y en cualquier caso se debe secar adecuadamente antes de iniciar los trabajos. Las conducciones de agua de refrigeración deben instalarse de forma que formen un bucle que permita gotear el agua de condensación o en caso de fuga. Los cables no deben someterse a corrientes por encima de su capacidad nominal ni enrollarse alrededor del cuerpo.
Utilización segura del material auxiliar de soldadura
La utilización segura del material de soldadura puede influir en la seguridad de los trabajos de soldadura. Se dan una serie de recomendaciones y prohibiciones relacionadas con la utilización.
- Recomendaciones
La base de soldar debe ser sólida y estar apoyada sobre objetos estables. El cable de soldar debe mantenerse con una mano y la soldadura se debe ejecutar con la otra. Los porta electrodos se deben almacenar donde no puedan entrar en contacto con los trabajadores, combustibles o posibles fugas de gas comprimido.
Cuando los trabajos de soldadura se deban interrumpir durante un cierto periodo se deben sacar todos los electrodos de los porta electrodos, desconectando el puesto de soldar de la fuente de alimentación.
No utilizar electrodos a los que les quede entre 38 y 50 mm; en caso contrario se pueden dañar los aislantes de los porta electrodos pudiendo provocar un cortocircuito accidental.
Los electrodos y sus porta electrodos se deben guardar bien secos. Si antes de ser utilizados están mojados o húmedos por cualquier razón, deben secarse totalmente antes de ser reutilizados.
Situarse de forma que los gases de soldadura no lleguen directamente a la pantalla facial protectora y proteger a los otros trabajadores del arco eléctrico mediante pantallas o mamparas opacas; llevar ropa, gafas y calzado de protección.
La escoria depositada en las piezas soldadas debe picarse con un martillo especial de forma que los trozos salgan en dirección contraria al cuerpo. Previamente se deben eliminar de las escorias las posibles materias combustibles que podrían inflamarse al ser picadas.
- Prohibiciones
No sustituir los electrodos con las manos desnudas, con guantes mojados o en el caso de estar sobre una superficie mojada o puesta a tierra; tampoco se deben enfriar los porta electrodos sumergiéndolos en agua.
No se deben efectuar trabajos de soldadura cerca de lugares donde se estén realizando operaciones de desengrasado, pues pueden formarse gases peligrosos. Tampoco se permitirá soldar en el interior de contenedores, depósitos o barriles mientras no hayan sido limpiados completamente y desgasificados con vapor. Es conveniente también prever una toma de tierra local en la zona de trabajo.
No accionar el conmutador de polaridad mientras el puesto de soldadura esté trabajando; se debe cortar la corriente previamente antes de cambiar la polaridad.
Equipo de protección individual
- Equipo y ropa
El equipo de protección individual está compuesto por: pantalla de protección de la cara y ojos; guantes de cuero de manga larga con las costuras en su interior; mandil de cuero; polainas; calzado de seguridad tipo bota, preferiblemente aislante; casco y/o cinturón de seguridad, cuando el trabajo así lo requiera.
La ropa de trabajo será de pura lana o algodón ignífugo. Las mangas serán largas con los puños ceñidos a la muñeca; además llevará un collarín que proteja el cuello. Es conveniente que no lleven bolsillos y en caso contrario deben poderse cerrar herméticamente. Los pantalones no deben tener dobladillo, pues pueden retener las chipas producidas, pudiendo introducirse en el interior del calzado de seguridad.
- Normas de utilización y mantenimiento
El soldador debe tener cubiertas todas las partes del cuerpo antes de iniciar los trabajos de soldadura. La ropa manchada de grasa, disolventes o cualquier otra sustancia inflamable debe ser desechada inmediatamente; asimismo la ropa húmeda o sudada se hace conductora por lo que debe también ser cambiada ya que en esas condiciones puede ser peligroso tocarla con la pinza de soldar. Por añadidura no deben realizarse trabajos de soldadura lloviendo, o en lugares conductores, sin la protección eléctrica adecuada. Antes de soldar se debe comprobar que la pantalla o careta no tiene rendijas que dejen pasar la luz, y que el cristal contra radiaciones es adecuado a la intensidad o diámetro del electrodo.
Los ayudantes de los soldadores u operarios próximos deben usar gafas especiales con cristales filtrantes adecuados al tipo de soldadura a realizar. Para colocar el electrodo en la pinza o tenaza, se deben utilizar siempre los guantes. También se usarán los guantes para coger la pinza cuando esté en tensión.
En trabajos sobre elementos metálicos, es necesario utilizar calzado de seguridad aislante. Para los trabajos de picado o cepillado de escoria se deben proteger los ojos con gafas de seguridad o una pantalla transparente.
En trabajos en altura con riesgo de caída, se utilizará un cinturón de seguridad protegido para evitar que las chispas lo quemen. El cristal protector debe cambiarse cuando tenga algún defecto (por ej. rayado) y ser sustituido por otro adecuado al tipo de soldadura a realizar. En general todo equipo de protección individual debe ser inspeccionado periódicamente y sustituido cuando presente cualquier defecto.
Mantenimiento e inspección del material
Se debe inspeccionar semanalmente todo el material de la instalación de soldadura, principalmente los cables de alimentación del equipo dañados o pelados, empalmes o bornes de conexión aflojados o corroídos, mordazas del porta electrodos o bridas de tierra sucias o defectuosas, etc.
En cuanto a los equipos de soldar de tipo rotativo es necesario revisar las escobillas sustituyéndolas o aproximándolas en caso necesario. En ambientes con polución se debe limpiar periódicamente el interior con aire comprimido para evitar cortocircuitos o derivaciones a la carcasa.
Referencias
- Instituto Nacional de Seguridad y Salud en el Trabajo – NTP 494: Soldadura eléctrica al arco: normas de seguridad.