Por María Camila Suárez Paba / Ingeniera Química / Magíster en Ingeniería Química / Doctora en Ingeniería – Universidad de Kioto (Japón) / Conocimiento y experiencia en desastres naturales que desencadenan accidentes industriales (Natech), medidas de prevención y mitigación para mejorar la capacidad de recuperación territorial a los riesgos Natech, seguridad de procesos y análisis cuantitativos de riesgos / Bogotá, Colombia / 2020.
¿Qué son los indicadores de desempeño?
Es claro para los propietarios o administradores de instalaciones peligrosas, que deben conocer los riesgos existentes en estas. Esto se logra a través de una cultura de seguridad conocida y aceptada en toda la empresa y a través de la implementación de un sistema de gestión de la seguridad, que se revise y actualice periódicamente. Lo anterior permite que las instalaciones industriales estén preparadas ante cualquier accidente que pueda ocurrir. Sin embargo, para lograr tal estado, es importante que las organizaciones se apoyen en indicadores de desempeño de seguridad de procesos que, si se monitorean, pueden usarse para limitar o prevenir incidentes relacionados con el proceso (OECD, 2008).
Es así como en la industria de procesos, los programas de mejora continua utilizan indicadores para medir el desempeño actual y futuro de sus procesos. Esto les permite obtener una mirada de las buenas prácticas y las oportunidades de mejora, lo que repercute en una mejora continua de la seguridad de sus operaciones (CCPS, 2011). Teniendo en cuenta lo anterior, es posible afirmar que los indicadores de desempeño son herramientas utilizadas para monitorear el cumplimiento de los objetivos de un sistema, proporcionando información sobre los niveles de seguridad. Estos indicadores pueden tener diversos enfoques, ser abordados desde una perspectiva de la salud y seguridad en el trabajo o desde una perspectiva de seguridad de procesos, los cuales no necesariamente tienen una relación directa. A su vez, pueden tener un carácter retrospectivo o prospectivo.
A pesar de las diversas alternativas existentes para plantear indicadores de desempeño, aún no se ha establecido una fórmula genérica que pueda ser adaptada a cualquier tipo de industria. Por lo tanto, la implementación de este tipo de indicadores depende de las características y particularidades de cada instalación industrial, sus procesos, sistemas de seguridad y cultura de seguridad de procesos, entre muchas otras variables. Es así que, tal como lo afirman Swuste y colaboradores, aún no se ha identificado la «solución milagrosa» en este sentido (Swuste et al., 2016).
Debido precisamente a las múltiples alternativas, existen también diversas definiciones que abordan desde diferentes aristas los indicadores de desempeño. La Tabla 1 muestra un paralelo sobre algunas de las definiciones de los indicadores de seguridad de procesos, propuestas por diferentes autores, tanto desde una óptica de la literatura científica como desde la literatura profesional. Esto sugiere que aún no existe un consenso en la definición, pero si se observa detenidamente, el enfoque abordado es el mismo; esto es, evaluar la efectividad con que un sistema controla sus riesgos, mediante el cumplimiento de objetivos previamente establecidos que contemplan aspectos organizacionales, del proceso y de la infraestructura.
Tabla 1. Definiciones de diversos autores sobre indicadores de seguridad de procesos. Adaptado de (Swuste et al., 2016)
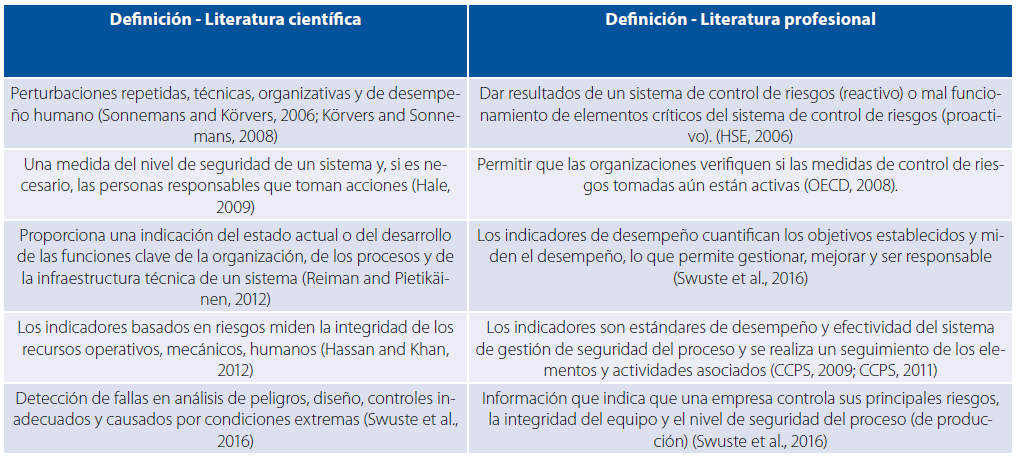
En la práctica, la gestión del desempeño se hace evidente en la selección de indicadores representativos que reflejen de forma realista el estado del entorno laboral y los procesos productivos. Por lo tanto, se utilizan para determinar qué tan alejado o cercano está el sistema de la situación óptima, de acuerdo con los estándares y objetivos definidos por el gerente de seguridad de procesos y su equipo. Pero la pregunta que surge entonces es ¿qué debe considerar una adecuada gestión del desempeño?, ¿indicadores retrospectivos, prospectivos o una combinación de ambos?
¿Indicadores retrospectivos, prospectivos o una combinación de ambos?
Los indicadores retrospectivos son precursores de incidentes de pérdida de contención, mientras que los indicadores prospectivos miden la calidad del sistema de gestión (Knegtering and Pasman, 2009; Zwetsloot, 2009). Otras definiciones establecen que los primeros se refieren a “medidas de la ocurrencia y frecuencia de eventos que ocurrieron en el pasado, como el número de lesiones, enfermedades y muertes” (OSHA, 2019). Los segundos, por su parte, se refieren a “medidas proactivas, preventivas y predictivas que brindan información sobre el desempeño efectivo de sus actividades de seguridad y salud; es decir, que miden los eventos que conducen a lesiones, enfermedades y otros incidentes y revelan problemas potenciales en su programa de seguridad y salud (OSHA, 2019)”. Nótese, sin embargo, la distinción entre las dos aproximaciones: por una parte, la primera definición hace referencia a la seguridad de procesos y por otra, la segunda definición tiene un enfoque en seguridad industrial, es decir, la seguridad al trabajador. Esto denota que existen dos dimensiones de los indicadores de seguridad, a saber: seguridad personal versus indicadores de seguridad del proceso. La distinción entre indicadores de seguridad personal y de procesos es relativamente clara, pero a la hora de hacer esta distinción entre los indicadores prospectivos y los reactivos, las cosas se tornan algo confusas (Hopkins, 2009).
Por lo anterior, resulta muy importante que esta diferencia esté claramente establecida cuando se trata de definir indicadores de desempeño. Lo anterior debido a que, de acuerdo con Hopkins, la seguridad industrial se enfoca en eventos de alta probabilidad, pero de baja consecuencia, como caídas o tropezones, mientras que la seguridad de procesos se concentra en eventos de baja probabilidad y alta consecuencia, como es el caso de incendios o explosiones (Hopkins, 2011). Lo anterior indica que el primero busca prevenir incidentes que puedan afectar a los trabajadores y el segundo prevenir un accidente mayor. Cabe mencionar que ambas aproximaciones no son mutuamente excluyentes y por el contrario son complementarias.
Lo importante de la discusión es la relación causal entre las mediciones de desempeño proactivas (indicadores prospectivos) y las mediciones de resultados (indicadores retrospectivos). Esto es, las condiciones de seguridad modificables y los resultados no deseados. De acuerdo con Dyreborg (2009) un enfoque proactivo sugiere que desde una mirada de la seguridad de procesos se deban considerar medidas de las causas fundamentales y el desempeño del proceso productivo, con lo cual se logre monitorear la condición de seguridad del sistema (Reason, 1997). Sin embargo, para lograrlo, los indicadores de desempeño necesariamente deben basarse en evidencia práctica o científica. Más allá de esta afirmación, resulta indiscutible el hecho de que los indicadores de seguridad de procesos pueden ser complejos, debido a que son dependientes de los escenarios y sus diversas maneras de desplegarse (Dyreborg, 2009; Bellamy, 2009; Kjellén, 2009).
Indicadores de desempeño y métricas
Precisamente debido a su complejidad, los indicadores de desempeño deben recurrir a valores medibles que permitan cuantificarlos. Para ello se hace uso de las métricas que definen el aspecto o elemento que se puede medir y su cuantificación. De esta manera, las métricas son mediciones de variables y/o eventos específicos. Dichas variables difieren dependiendo de las características de cada compañía u organización, el enfoque en seguridad industrial o seguridad de procesos y sus condiciones del proceso productivo, entre otros aspectos. Por lo tanto, las métricas responden a las especificidades, requerimientos y expectativas de cada empresa (Muñoz Giraldo et al., 2015).
Bajo el enfoque de la seguridad de procesos, tanto los incidentes como los casi- incidentes suelen ser criterios relevantes para evaluar la efectividad de las medidas de seguridad implementadas. Esto es así debido a que la sucesiva ocurrencia de este tipo de escenarios, al igual que un comportamiento inseguro o una disciplina operativa insuficiente, suelen preceder a la ocurrencia de un accidente mayor (CCPS, 2009). Por lo tanto, las métricas de seguridad de procesos han sido un área de gran interés para mejorar el desempeño de la seguridad en la industria, porque su uso permite identificar problemas o fallas que puedan provocar un incidente de seguridad de procesos y corregirlo. De acuerdo con Lord Kelvin (1824-1907) «Si no puedes medirlo, no puedes mejorarlo» (CCPS, 2009), afirmación que es completamente válida si se considera que las métricas permiten medir dónde hay oportunidades de mejora o se necesita intervención y dónde existen buenas prácticas. Pero esta visión debe ir acompañada de una toma de decisiones e implementación de medidas basadas en los resultados de las métricas. Bajo esta mirada, es preciso mencionar que existen diferentes aproximaciones definidas por organizaciones como CCPS (Center of Chemical Process Safety) o la OECD (Organisation for Economic Cooperation and Development) (CCPS, 2009; CCPS, 2011; OECD, 2008). A pesar de ello, tal como se muestra en la Tabla 2, se conservan factores clave que se pueden tipificar en tres grupos principales.
Tabla 2. Grupos principales que tipifican las métricas a nivel industrial. Tomado de (Muñoz Giraldo et al. 2015)}
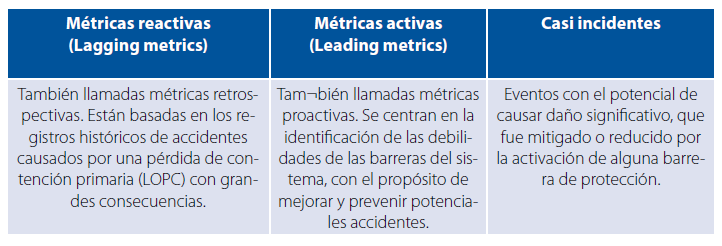
Estas métricas y su registro permiten obtener información clave acerca de las causas, consecuencias, desempeño, problemas recurrentes y problemas potenciales para soportar la toma de decisiones e implementar las medidas de reducción de riesgo pertinentes. Sin embargo, es indispensable que el uso de las métricas no se enfoque netamente en aquellas de carácter retrospectivo, sino que, como se ha mencionado, exista un equilibrio con aquellas de carácter prospectivo. Esto repercute en una mejora continua del desempeño de las compañías, teniendo en cuenta que se están evaluando continuamente situaciones ocurridas previamente y posibles eventos futuros, fortaleciendo las lecciones aprendidas. Esta combinación de métricas robustece al sistema, dado que ayuda a las compañías a tener una visión de futuro, en lugar de simplemente enfocarse en analizar lo que ha salido mal. Por lo anterior, esta combinación potencialmente resulta en tasas de incidentes o casi incidentes mucho más bajas. Con esto en mente, el uso de métricas y procedimientos de gestión del cambio también contribuye a detectar si las medidas de reducción de costos han afectado o afectarán la seguridad, o dónde se necesitan mejoras en el programa de seguridad (CCPS, 2009).
Finalmente, y de la mano con lo expuesto, es importante que tanto el uso de los indicadores como de sus métricas esté cobijado bajo una cultura de seguridad de procesos sólida, que defina claramente sus expectativas e intolerancia a la desviación respecto al buen desempeño de la seguridad de procesos.
Lecciones aprendidas en la implementación de indicadores de desempeño en la industria
El 23 de marzo de 2005 la refinería de BP en la ciudad de Texas experimentó uno de los accidentes industriales más graves en la historia reciente de los Estados Unidos. Como consecuencia de errores durante la puesta en marcha de una torre divisora de refinado en la unidad de isomerización. El problema se ocasionó por el bombeo de hidrocarburos líquidos inflamables a la torre durante más de tres horas, generando un exceso de líquido que desbordó la tubería superior, debido a que los sistemas de alarma e instrumentación de control no estaban funcionando correctamente. Esto aumentó la presión en la parte inferior y por ende fue necesario abrir las tres válvulas de alivio de presión, descargando una gran cantidad de líquido inflamable a un tambor de purga con una chimenea de ventilación abierta a la atmósfera. Sin embargo, el sistema de purga no estaba conectado
El 23 de marzo de 2005 la refinería de BP en la ciudad de Texas experimentó uno de los accidentes industriales más graves en la historia reciente de los Estados Unidos. Como consecuencia de errores durante la puesta en marcha de una torre divisora de refinado en la unidad de isomerización. El problema se ocasionó por el bombeo de hidrocarburos líquidos inflamables a la torre durante más de tres horas, generando un exceso de líquido que desbordó la tubería superior, debido a que los sistemas de alarma e instrumentación de control no estaban funcionando correctamente. Esto aumentó la presión en la parte inferior y por ende fue necesario abrir las tres válvulas de alivio de presión, descargando una gran cantidad de líquido inflamable a un tambor de purga con una chimenea de ventilación abierta a la atmósfera. Sin embargo, el sistema de purga no estaba conectado a una antorcha que contuviera de manera segura los líquidos y los vapores inflamables liberados del proceso. Por lo tanto, el líquido volátil liberado se evaporó al caer al suelo y formó una nube de vapor inflamable, que, posteriormente encontró una fuente de ignición cercana desencadenando en explosiones e incendios. Como consecuencia 15 contratistas fallecieron, se reportaron más de 180 lesiones, pérdidas económicas superiores a los USD$ 1,5 mil millones y se emitió una orden de refugio en el lugar que requirió que 43.000 personas permanecieran en el interior (CSB, 2007).
Como resultado de las investigaciones de la Chemical Safety Board (CSB), una agencia federal independiente encargada de investigar los accidentes químicos industriales, se encontró que existían serios problemas en cuanto a: 1) la efectividad del sistema de gestión de seguridad, 2) la efectividad de la supervisión de seguridad corporativa y 3) una cultura de seguridad corporativa con graves desviaciones respecto a la tolerabilidad de las buenas prácticas de seguridad (Baker et al., 2007). Estos elementos cruciales fueron corroborados al identificar que la refinería de BP Texas City había experimentado otros dos incidentes de seguridad fatales en 2004, un gran incendio de hidrógeno relacionado con el proceso el 28 de julio de 2004 y otro incidente grave el 10 de agosto de 2004 (Baker et al., 2007). Esto sólo sugiere que en repetidas ocasiones la compañía tuvo alarmas y señales de advertencia, pero que la empresa no intervino de manera efectiva para prevenir la materialización de los eventos previamente mencionados.
De acuerdo con las investigaciones, dentro de los muchos factores y causas que generaron el accidente en la refinería de Texas se incluyen deficiencias organizacionales y de seguridad en todos los niveles corporativos. Ejemplo de ello fue el hecho de que la compañía utilizó como métrica una tasa de lesiones personales muy baja, generando una falsa confianza y enviando un mensaje distorsionado del real desempeño de la instalación. Como resultado, BP soportó su toma de decisiones sobre el desempeño de seguridad del proceso en un indicador engañoso. Aunado a lo anterior, la CSB también pudo corroborar que el programa general de cultura y gestión de la seguridad de procesos presentaba graves deficiencias (CSB, 2007). Por otra parte, el reporte también indica que dentro de los hallazgos clave respecto a los aspectos organizacionales, se encontró que los objetivos de seguridad se enfocaban en mejorar la seguridad industrial y el comportamiento de los trabajadores, dejando de lado un enfoque en la seguridad de procesos y su gestión.
Lo anterior demuestra la importancia de que las compañías tengan un balance entre los indicadores retrospectivos y prospectivos. De acuerdo con el análisis de Hopkins, empresas como BP no deberían asumir que los indicadores de seguridad industrial son al mismo tiempo medidas de seguridad de procesos y por lo tanto es necesario que desarrollen indicadores de seguridad de procesos específicos (Hopkins, 2009). Se infiere, por lo tanto, que un enfoque prospectivo aumenta la probabilidad y capacidad de la industria para medir, monitorear y detectar condiciones de seguridad y evaluar el desempeño de los procesos productivos, identificando deterioros o posibles fallas futuras (Baker et al., 2007).
Ahora bien, BP tenía indicadores como número de días sin accidentes laborales, lo cual es válido y aceptable desde el punto de vista de la seguridad industrial. El problema radica en que se tomen decisiones de seguridad de procesos utilizando solamente estos indicadores enfocados en la seguridad de los trabajadores. Por esta razón, dentro de las recomendaciones a la BP se sugirió que se debía desarrollar un indicador retrospectivo que considerara el número de incidentes relacionados con el proceso, es decir, incendios, explosiones, incidentes de pérdida de contención de materiales peligrosos y lesiones relacionadas con el proceso (Hopkins, 2009; Baker et al., 2007). Esta visión, tal como se planteó en el informe del panel Baker, habría permitido a la BP cuantificar los numerosos incidentes de procesos ocurridos en años y meses anteriores, permitiéndole priorizar la intervención para reducir el número de fallas y reducir las cifras de accidentalidad. Es así, como cualquier mejora en este índice compuesto habría sido indicativo de mejoras en el sistema de gestión de seguridad en la refinería de Texas (Hopkins, 2009; Baker et al., 2007).
Reflexiones finales
El panorama general presentado sobre los indicadores de desempeño en la industria y el paralelo entre el enfoque en seguridad industrial y seguridad de procesos muestra que, si bien la implementación y uso de indicadores de desempeño y sus métricas se ha venido desarrollando desde hace varios años, es evidente que aún existe confusión entre los diferentes enfoques y su utilidad. Es claro que las compañías necesitan indicadores simples, comprensibles y comunicables tanto para el enfoque en seguridad de procesos como en seguridad industrial, al igual que aquellos de carácter retrospectivo y prospectivo. Es evidente que el uso complementario de los indicadores de desempeño retrospectivos y prospectivos fortalece al sistema de seguridad. Por un lado, los indicadores retrospectivos, generados por un proceso de monitoreo reactivo, permiten realizar un seguimiento de eventos no deseados; por otro lado, los indicadores prospectivos, resultado de un monitoreo activo, conllevan pruebas e inspecciones de rutina y planificadas.
Por lo tanto, la importancia de los indicadores de desempeño radica en varios aspectos. En primer lugar, proveen alertas tempranas para prevenir la ocurrencia de eventos accidentales. Este enfoque proactivo permite a las empresas encaminar esfuerzos para reducir la probabilidad de los accidentes y mejorar la preparación y la capacidad de respuesta. En segundo lugar, los indicadores de desempeño permiten un monitoreo frecuente del sistema, soportando así la confiabilidad de este. En tercer lugar, tienen la capacidad de evitar los costos directos asociados con la ocurrencia de accidentes e incidentes, al identificar oportunidades de mejora en cuanto a la eficiencia general de las operaciones. Y, en cuarto lugar, repercuten en la buena reputación de las empresas, una mejor comunicación y cooperación entre las empresas y las autoridades públicas, y un mejor relacionamiento con las comunidades vecinas.
En este orden de ideas, cualquier compañía o empresa que presente un riesgo de accidente con productos químicos peligrosos, independientemente de su ubicación, tamaño, naturaleza o propiedad, debe considerar la implementación de indicadores de desempeño de seguridad. Ahora bien, en el marco del contexto colombiano, esta visión resulta muy pertinente debido a la transformación normativa que se está dando en el país en materia de riesgo tecnológico y riesgo mayor. Esto se ve reflejado en el Programa de Prevención de Accidentes Mayores -PPAM-, cuyo propósito es la protección de los trabajadores, la población, el ambiente y la infraestructura ante escenarios de accidentes mayores, mediante la gestión del riesgo de sustancias químicas usadas en instalaciones industriales en el territorio nacional y la preparación y respuesta cuando estos ocurran. El PPAM dentro de sus componentes incluye el Sistema de Gestión de la Seguridad para la Prevención de Accidentes Mayores, el cual a su vez invita a que los responsables de las instalaciones peligrosas conciban dentro de sus sistemas de gestión, entre otros elementos, indicadores de desempeño que orienten el monitoreo, implementación y seguimientos de las medidas de reducción de riesgos.
Por lo tanto, esta será una oportunidad para que los indicadores retrospectivos y prospectivos se implementen en las instalaciones clasificadas que actualmente no estén haciendo uso de estos, o que se fortalezcan en aquellas instalaciones que ya tienen un sistema de seguridad industrial y de procesos consolidado que hace uso de dichos indicadores.
Referencias
- Baker, J., Bowman, F. L., Erwin, G., Gorton, S., Hendershot, D., Priest, S., Leveson, N., Rosenthal, I., Tebo, P., Wiegmann, D. and Wilson, L. (2007) The report of the BP US refineries independent safety review panel.
- Bellamy, L. J. (2009) ‘Process safety indicators: Response to Andrew Hopkins’, Safety Science, 47(4), pp. 472-473.
- CCPS (2009) Guidelines for Process Safety Metrics. New York.
- CCPS 2011. Process Safety Leading and Lagging Metrics.
- CSB (2007) Investigation Report: Refinery Explosion and Fire, Texas2005-04-I-TX). Available at: https://www.hsdl.org/?view&did=234995.
- Dyreborg, J. (2009) ‘The causal relation between lead and lag indicators’, Safety Science, 47(4), pp. 474-475.
- Hale, A. (2009) ‘Why safety performance indicators?’, Safety Science, 47(4), pp. 479-480.
- Hassan, J. and Khan, F. (2012) ‘Risk-based asset integrity indicators’, Journal of Loss Prevention in the Process Industries, 25(3), pp.544-554.
- Hopkins, A. (2009) ‘Thinking about process safety indicators’, Safety Science, 47, pp. 460– 465.
- Hopkins, A. 2011. WP 79 – Management walkarounds: Lessons from the Gulf of Mexico oil well blowout. Canberra: National Research Centre for OHS Regulation.
- HSE (2006) Developing process safety indicators: A step-by-step guide for chemical and major hazard industries.
- Kjellén, U. (2009) ‘The safety measurement problem revisited’, Safety Science, 47(4), pp. 486-489.
- Knegtering, B. and Pasman, H. J. (2009) ‘Safety of the process industries in the 21st century: A changing need of process safety management for a changing industry’, Journal of Loss Prevention in the Process Industries, 22(2), pp. 162-168.
- Körvers, P. M. W. and Sonnemans, P. J. M. (2008) ‘Accidents: A discrepancy between indicators and facts!’, Safety Science, 46(7), pp. 1067-1077.
- Muñoz Giraldo, F., Amaya Gómez, R., Romero Bayona, R. P. and Arbeláez Naranjo, C. I. 2015. NOTAS DE CLASE: Conceptos generales de seguridad de procesos. Módulos para la formación de ingenieros en temas relacionados con seguridad de proceso Ecopetrol S.A./ Uniandes.
- OECD 2008. Guidance on Developing Safety Performance Indicators Related to Chemical Accident Prevention, Preparedness and Response. Guidance for Industry. Second Edition ed. Paris: OECD Environment, Health and Safety Publications.
- OSHA 2019. Using Leading Indicators to Improve Safety and Health Outcomes.
- Reason, J. T. (1997) Managing the risks of organizational accidents. England: Ashgate.
- Reiman, T. and Pietikäinen, E. (2012) ‘Leading indicators of system safety – Monitoring and driving the organizational safety potential’, Safety Science, 50(10), pp. 1993-2000.
- Sonnemans, P. J. M. and Körvers, P. M. W. (2006) ‘Accidents in the chemical industry: are they foreseeable?’, Journal of Loss Prevention in the Process Industries, 19(1), pp. 1-12.
- Swuste, P., Theunissen, J., Schmitz, P., Reniers, G. and Blokland, P. (2016) ‘Process safety indicators, a review of literature’, Journal of Loss Prevention in the Process Industries, 40, pp. 162-173.
- Zwetsloot, G. I. J. M. (2009) ‘Prospects and limitations of process safety performance indicators’, Safety Science, 47(4), pp. 495-497.
Artículo técnico tomado de la Revista del Consejo Colombiano de Seguridad, Protección & Seguridad No. 394 Enero – Febrero 2021