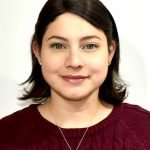
Tras varias semanas en cuarentena obligatoria, el gobierno nacional comienza a reactivar la vida productiva mediante la emisión de normativa que poco a poco habilita el retorno de algunos sectores. Esto permite la reactivación de ciertas instalaciones industriales, que por la naturaleza de sus procesos implican operaciones con riesgo de generar accidentes a causa de las sustancias químicas, condiciones de operación, los equipos y en general los peligros inherentes a los procesos industriales.
Cuando se está hablando de seguridad de procesos, se observa que uno de los momentos más críticos, es el arranque post-parada, independiente de cuál sea el motivo de la parada. Uno de los momentos en los cuales puede existir más riesgo de materialización de un accidente es después de la suspensión total de las actividades productivas de una planta, caso que se vive actualmente debido a la situación generada por la COVID-19, pues algunas instalaciones en el país detuvieron sus actividades obedeciendo a los lineamientos gubernamentales. Hoy en día, teniendo en cuenta la reactivación progresiva de algunos sectores industriales, cobra especial importancia seguir lineamientos de seguridad de procesos para evitar que se presenten accidentes mayores.
La industria en el mundo está viviendo una situación de reactivación económica generalizada y si no se toman las medidas preventivas correspondientes, se pueden presentar eventos accidentales con consecuencias importantes. Algunos ejemplos de lo que puede suceder durante el momento previo al arranque de una planta, lastimosamente se han presentado en los países que comienzan con la reactivación de sus actividades industriales; a continuación se describen dos eventos ocurridos el pasado 7 de mayo de 2020 en India.
En la ciudad de Visakhapatnam en India, una instalación de fabricación de polímeros que llevaba fuera de funcionamiento más de 40 días programó el retorno a las operaciones de una antigua planta de producción, tras la flexibilización de las restricciones para operar por parte del gobierno. Durante las actividades previas de inspección de los equipos, para su posterior puesta en marcha, se presentó una fuga de estireno en las horas de la noche, ante la cual los trabajadores presentes dieron la alarma y evacuaron sin resultar lastimados. Sin embargo, la fuga de la sustancia no pudo ser controlada hasta horas más tarde, llevando a que sus vapores alcanzaran varias poblaciones cercanas, resultando en la exposición de al menos 1.000 personas en la zona, siendo los niños y los adultos mayores los más afectados. En los hospitales del área fueron atendidas al menos 20 personas en condición crítica, con un total de más de 400 hospitalizados con dificultad respiratoria e irritación ocular, algunos de los cuales incluso ingresaron inconscientes. Se reportó el fallecimiento de al menos 11 personas, incluyendo dos que sufrieron un accidente mientras trataban de escapar para no exponerse a los vapores. El Gobierno indio indicó que afortunadamente pudieron ser atendidos todos los pacientes debido al stock de oxígeno y ventiladores que se tienen en los hospitales como respuesta a la pandemia que se vive a nivel mundial. Los equipos de atención de emergencias han indicado que entre 200 y 250 familias han sido evacuadas en un radio de unos 5 km, también se ha reportado la muerte de animales domésticos, ganado y aves de la zona. Se ha indicado que, si bien el gas no es extremadamente tóxico, produce efectos adversos tras la exposición prolongada. La empresa ha anunciado el inicio de una investigación para aclarar lo sucedido con más detalles (Archana Chaudhary, Sudhi Ranjan Sen, 2020; Indian express, 2020).
El mismo día ocurrió otro accidente en una compañía del sector papelero en India, en la ciudad de Raigarh. En el marco del retorno a las operaciones se programó la limpieza de un tanque abierto, puesto que la instalación llevaba semanas fuera de funcionamiento. Durante este procedimiento se presentó una fuga de un gas tóxico, la cual afectó a 7 trabajadores que tuvieron que ser remitidos a hospitales de la zona, al menos 3 de ellos en estado crítico. En este caso, el responsable de la instalación no reportó el incidente y las autoridades conocieron el caso debido a la presencia de los afectados en los hospitales. A la fecha, se indicó que las autoridades iniciaron la investigación de lo sucedido y se encuentran interrogando al responsable de la instalación (Mishra, 2020; Times Now Digital, 2020).
Debido a la gravedad de esta clase de eventos, es fundamental que los gobiernos definan lineamientos de seguridad para ayudar a la prevención de accidentes de este tipo, sobre todo en situaciones como las que se están viviendo actualmente a nivel global considerando los impactos sociales y económicos de la crisis en la implementación de medidas para que la producción se reinicie prontamente. Colombia ha tenido en cuenta las experiencias de otros países enfrentando la pandemia un par de meses antes y ha aprendido lecciones de éstas. En ese mismo orden de ideas, el país debe tomar las experiencias internacionales de los países que han comenzado el proceso de reactivación de la economía y prepararse para las situaciones que pueden presentarse en el territorio nacional.
De los casos ocurridos se puede resaltar la importancia de la seguridad de procesos antes y durante las operaciones y la comunicación del riesgo para que las comunidades se encuentren preparadas, conociendo los riesgos a los cuales se encuentran expuestas y cómo deben proceder en caso de ocurrido un evento, minimizando sus consecuencias en la medida de lo posible.
Las investigaciones de los accidentes sucedidos mostrarán las causas del evento, la dinámica de los eventos que derivaron en el accidente, cuáles fueron los errores que se cometieron y las oportunidades de mejora en los procesos para ayudar a mejorar los niveles de seguridad en las instalaciones.
De manera general, las paradas de planta durante periodos prolongados pueden presentar un desafío cuya complejidad aumenta en las circunstancias actuales, cuyas particularidades pueden resumirse en algunos puntos de especial interés. El primer punto para tener en cuenta es que iniciar operaciones tras largos periodos de parada total puede representar un desafío, teniendo en cuenta el incremento de la probabilidad de que se presente un incidente durante el arranque post-parada (CCPS, 2007). Lo anterior se debe a que durante este tiempo no necesariamente se hace seguimiento a los equipos del proceso y su estado, no se realizan labores de mantenimiento y los operadores, al estar fuera del proceso tanto tiempo, pueden perder algo de habilidad con sus tareas; además, se pueden haber producido derrames e incluso fallas que amenazan la integridad de los equipos. Debido a esto, los sistemas de gestión de seguridad de procesos tienen un elemento que se centra en las revisiones de seguridad antes de retornar a la operación y otros elementos asociados que lo soportan, sobre los cuales se ampliará la información más adelante.
El segundo elemento es que teniendo en cuenta las circunstancias actuales, algunas industrias pueden haber visto reducida su productividad, llevando a recortes presupuestales que limiten así la disponibilidad de recursos (servicios, materiales, equipos) para las medidas de seguridad a tomar. El tercer punto, relacionado con el anterior, se refiere a que en la organización pueden haberse presentado despidos o disminución de la dedicación del personal encargado de la seguridad, debido a los recortes presupuestales. Los elementos mencionados se vuelven de vital importancia en este momento, teniendo en cuenta que el Gobierno nacional ha anunciado el retorno progresivo a la vida productiva. El Centro para la Seguridad de Procesos (CCPS por sus siglas en inglés)[1] del Instituto Americano de Ingenieros Químicos (AIChE por sus siglas en inglés)[2], ha desarrollado algunas recomendaciones para incrementar los niveles de seguridad en las instalaciones que operan durante estos tiempos. Estas fueron desarrolladas en el marco del Sistema de Gestión de Seguridad de Procesos (RBPS por sus siglas en inglés)[3] (CCPS, 2007) el cual consta de 20 elementos (agrupados en 4 pilares), pero aplican de manera general para cualquier tipo de instalación industrial, independientemente de si tiene o no implementado un Sistema de Gestión de Seguridad de Procesos.
Es de particular importancia tener consideraciones con respecto a la gestión del recurso humano, pues en una situación de crisis se convierte en uno de los mayores desafíos. Las personas se encuentran particularmente expuestas a situaciones de ansiedad, estrés y fatiga, lo que puede disminuir su rendimiento y su atención al detalle, llevando incluso a incrementar la probabilidad de cometer fallas que desencadenen incidentes. Estos aspectos se abordan en los siguientes elementos del sistema de gestión: cultura de seguridad de procesos, alcance de interés y conducción de operaciones (CCPS, 2020).
Es importante recordar que ahora, más que nunca, la seguridad de las instalaciones no puede ser dejada de lado, por lo que a continuación se presentan algunas medidas generales para las circunstancias especiales que representa retomar los procesos en la actualidad, tras largos periodos de parada y con recursos que pueden haberse visto disminuidos. Es importante recordar que estas recomendaciones son un complemento al Sistema de Gestión de Seguridad de Procesos para la situación actual y su implementación no constituye el sistema de gestión propiamente dicho. En la tabla se ven resaltadas en negrilla aquellas recomendaciones que CCPS considera más críticas. El CCS propone algunas medidas complementarias (en cursiva) que se articulan con los Sistemas de Gestión de la Seguridad y Salud en el Trabajo (SG-SST) que las empresas en Colombia deben tener implementados, de acuerdo con el Decreto 1072 de 2015.
[1] CCPS: Center for Chemical Process Safety [2] AIChE: American Institute of Chemical Engineers [3] RBPS: Risk-Based Process SafetyTabla 1. Recomendaciones en tiempos disruptivos, de acuerdo con los elementos RBPS. Adaptado de (CCPS, 2020)
Seguridad de Procesos Basada en Riesgo de CCPS con perspectivas para tiempos disruptivos |
||
1 | Cultura de seguridad de procesos |
|
2 | Cumplimiento con las normas |
|
3 | Capacidad laboral en Seguridad de Procesos |
|
4 | Participación de la fuerza laboral |
|
5 | Alcance a grupos de Interés |
|
6 | Gestión del conocimiento |
|
7 | Identificación de Peligros y Análisis de Riesgos (HIRA) |
|
8 | Procedimientos operacionales |
|
9 | Prácticas laborales seguras |
|
10 | Integridad y confiabilidad de activos |
|
11 | Gestión de Contratistas |
|
12 | Capacitación |
|
13 | Gestión de cambios |
|
14 | Disponibilidad operacional |
|
15 | Conducción de operaciones |
|
16 | Gestión de emergencias |
|
17 | Investigación de incidentes |
|
18 | Métricas |
|
19 | Auditoría |
|
20 | Revisión gerencial y mejora continua |
|
Cabe resaltar que las recomendaciones anteriores son complementarias a las directrices normales del Sistema de Gestión de Seguridad de Procesos y del SG-SST, sin embargo, tenerlas en cuenta independientemente del nivel de implementación de su sistema de gestión, puede ayudar a incrementar los niveles de seguridad en sus instalaciones industriales, por lo que en estos momentos no deben perder de vista los siguientes aspectos:
- Cuide la salud física y mental de las personas, manteniéndolas informadas y transmitiendo tranquilidad en la medida de lo posible, demostrando el interés de la alta dirección en su bienestar.
- No olvide que la seguridad no da espera, por lo que debe revisar muy bien la reducción de recursos en temas de seguridad y sus posibles consecuencias.
- Considere la flexibilidad en la asignación de carga laboral en la medida de las posibilidades. No pierda de vista que algunos de sus trabajadores han visto incrementada su carga de trabajo en casa, algunos de ellos incluso deben ejercer múltiples roles: padres, profesores, cuidadores de enfermos, encargados de las labores de casa y trabajadores.
- Priorice los recursos económicos, reconsiderando aquello que es realmente urgente y aquello que es importante, teniendo en cuenta sus implicaciones en la seguridad de las instalaciones.
- Considere aplazar actividades en la medida que no afecten la seguridad de la instalación y los procesos.
La situación económica es complicada, sin embargo, se debe recordar que prevenir siempre es mejor que lamentar. Un accidente en una instalación industrial, puede resultar en personas lesionadas, fatalidades, pérdidas en producción, contaminación ambiental, llevando incluso a amenazar la continuidad del negocio. Es por esto que las inversiones en temas de seguridad deben ser analizadas con un retorno de inversión teniendo en cuenta los costos evitados en la materialización de un accidente grave incluyendo el costo de las vidas perdidas, las pérdidas económicas y las responsabilidades legales derivadas del evento.
Referencias
- Archana Chaudhary, Sudhi Ranjan Sen, and K. K. (2020). At Least Eleven Dead, Thousands Evacuated in India Gas Leak. Bloomberg. https://www.bloomberg.com/news/articles/2020-05-07/seven-dead-thousands-evacuated-in-overnight-gas-leak-in-india
- CCPS. (2007). Guidelines for Risk-based Process Safety. John Wiley & Sons, Inc.
- CCPS. (2020). Monografía de CCPS: seguridad de procesos basado en riesgo en tiempos disruptivos.
- Indian express. (2020). No TitleVizag gas leak: 11 dead, state govt announces Rs 1 crore compensation each to kin of dead. https://indianexpress.com/article/india/visakhaptnam-lg-polymers-gas-leakage-live-updates-6397737/
- Mishra, R. (2020). Seven workers fall ill after gas leak in Chhattisgarh’s paper mill. Hindustan Times. https://www.hindustantimes.com/india-news/seven-workers-fall-ill-after-gas-leak-in-chhattisgarh-s-paper-mill/story-US6cfko6pvoEA8zKnG9tKJ.html
- Times Now Digital. (2020). Chhattisgarh: 7 hospitalised, 3 critical after gas leak at paper mill in Raigarh; owner tried to hide incident. https://www.timesnownews.com/india/article/chhattisgarh-7-hospitalised-3-in-critical-condition-after-gas-leak-at-paper-mill-in-raigarh/588418