Por Andrés Camilo Hernández Salamanca / Asesor Técnico de CISPROQUIM® / Consejo Colombiano de Seguridad (CCS) / enero 2020 / Bogotá, Colombia.
Cómo citar este artículo:
Hernández,AO. (2020). Jerarquía de controles para reducir la exposición a productos químicos. Revista Protección & Seguridad. pág. 47-54. Consejo Colombiano de Seguridad. https://ccs.org.co/portfolio/jerarquia-de-controles-para-reducir-la-exposicion-a-productos-quimicos/
Introducción
Dentro de la gestión que realiza una empresa, sin importar su actividad económica, debe garantizar diferentes factores como el cumplimiento de estándares de calidad, el aumento de la productividad, manejar una imagen favorable interna y externa, proporcionar un ambiente seguro, entre otros; sin embargo, cuando se trata de compañías las cuales producen, manejan, distribuyen, almacenan o dentro de su proceso está involucrada una sustancia química, toma gran importancia el propender por un ambiente seguro debido a que los productos y/o las sustancias químicas pueden presentar características intrínsecas que tengan algún potencial de causar afectaciones a la salud de los trabajadores, al ambiente o a las instalaciones (Martín Penella, 2014).
En consecuencia, dentro de una empresa que en sus actividades exponga a los trabajadores a productos químicos, se debe realizar una gestión detallada referente a la seguridad y salud en el trabajo, la cual esté directamente enfocada en la higiene industrial, la seguridad industrial y la seguridad de procesos, y que permita informar, capacitar, proteger y brindar un entorno seguro y saludable a los trabajadores (Organización Internacional del Trabajo, 2014). Por esa razón, teniendo en cuenta la normatividad colombiana relacionada con el Sistema de Gestión de Seguridad y Salud en el Trabajo, en el artículo 2.2.4.6.7. del Decreto 1072 de 2015 del Ministerio del Trabajo, se establece que las empresas dentro de su Política de Seguridad y Salud en el Trabajo (SST) deben tener como uno de los objetivos el de “realizar la identificación de los peligros, evaluar y valorar los riesgos y establecer los respectivos controles”, con el fin de proteger la seguridad y la salud de todos los trabajadores (Ministerio del Trabajo, 2017).
De esta forma, como primer paso se debe realizar una búsqueda detallada de todas las situaciones o fuentes las cuales podrían causar daños a los trabajadores tales como lesiones, accidentes, enfermedades laborales e incluso fatalidades. Es por esto que se hace determinante realizar una adecuada observación, inspección y auditorias del sitio de trabajo, un análisis de seguridad laboral, un análisis de accidente previos, entre otras alternativas que permitan identificar los peligros a los cuales están expuestos los trabajadores (EMC Insurance Companies, 2013). Seguido a eso, se hace indispensable realizar una evaluación del riesgo que tiene cierto peligro sobre el trabajador, teniendo en cuenta factores como la probabilidad de que ocurran y el impacto que tienen en caso de que se presente el evento; dando como resultado generalmente una matriz que determina el nivel de riesgo y lo cataloga como bajo, moderado o alto.
Determinación de controles
Al tener identificados los peligros y evaluar los riesgos a los cuales están expuestos los trabajadores, se deben tomar una serie de medidas tanto preventivas como correctivas, las cuales permitan controlar los peligros identificados y corregir las condiciones inseguras en los lugares de trabajo; considerando que al momento de establecer los controles se deben priorizar aquellos riesgos valorados como moderados y altos (“Controlling risks – WorkSafeBC,” n.d.). En la figura 1, se ilustra un ejemplo de matriz de evaluación de riesgos y se señalan los niveles que deben ser prioritarios para su control.
Figura 1. Matriz de evaluación de riesgos. Fuente (adaptado de): Controlling risks – WorkSafeBC. (n.d.).
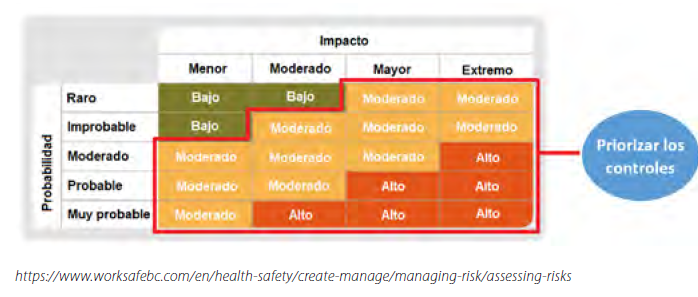
De manera que, para realizar el control de los riesgos valorados, como primera medida se debe establecer si los controles que actualmente se están ejecutando dentro de la compañía son los adecuados para reducir o mitigar la exposición de los trabajadores a los peligros, o si por el contrario se requiere de la implementación de nuevos controles más eficaces para la prevención de enfermedades laborales o incidentes. Debido a lo anterior, en caso de que se requiera de nuevos controles, se debe realizar una búsqueda exhaustiva de todas las posibilidades que se puedan aplicar para realizar esta labor. Sin embargo, se puede llegar a tener un sinnúmero de opciones por las cuales se puede abordar el riesgo, y por esta razón en ocasiones existe la probabilidad de seleccionar un control que no proteja de forma efectiva al trabajador.
Jerarquía de controles
Por consiguiente, antes de seleccionar el control que sea más idóneo, se debe tener en cuenta toda la reglamentación pertinente en la cual se indique de forma específica la manera o el método con el cual se debe hacer el tratamiento y el control de los riesgos (Canadian Centre for Occupational Health and Safety, 2018). Si no existe alguna normatividad que regule el peligro a controlar, se debe adoptar una metodología la cual de forma sistémica permita aplicar un orden de prioridades en la búsqueda de medidas de control y de esta manera aumentar la protección, la seguridad y la salud a los trabajadores; en ese sentido se ha instaurado la jerarquía de controles de riesgos la cual clasifica los posibles controles en un orden decreciente según su efectividad.
La jerarquía de controles define cinco herramientas que se encuentran posicionadas de acuerdo a un orden de prioridad con el objetivo de reducir los riesgos al nivel más bajo posible, de ahí que, según la jerarquía de controles, la medida con mayor efectividad es la eliminación de los peligros y la medida que tiene un menor grado de efectividad es la protección de los trabajadores al peligro por medio de Elementos de Protección Personal (EPP). Del mismo modo, a fin de establecer la funcionalidad de los diferentes tipos de controles, se ha planteado una clasificación la cual agrupa varios controles dependiendo de la causa o fuente a la cual se le va a aplicar el control; por un lado, se tienen los “controles duros” los cuales están directamente enfocados a realizar la eliminación o la reducción del peligro, y se encuentran conformados por los controles denominados como “Eliminación”, “Sustitución” y “Controles de ingeniería”; por el otro lado, se establecen los “controles blandos” que buscan reducir el riesgo o reducir la exposición de los trabajadores a los peligros, teniendo en este grupo los “Controles Administrativos” y los “Elementos de Protección Personal (EPP)” (Liberati, Peerally, & Dixon-Woods, 2018). En la figura 2 se ilustra la pirámide invertida correspondiente a la jerarquía de controles.
Figura 2. Jerarquía de controles. Fuente (traducido de): CDC – Hierarchy of Controls – NIOSH Workplace Safety and Health Topic. (2015). https://www.cdc.gov/niosh/topics/hierarchy/default.html
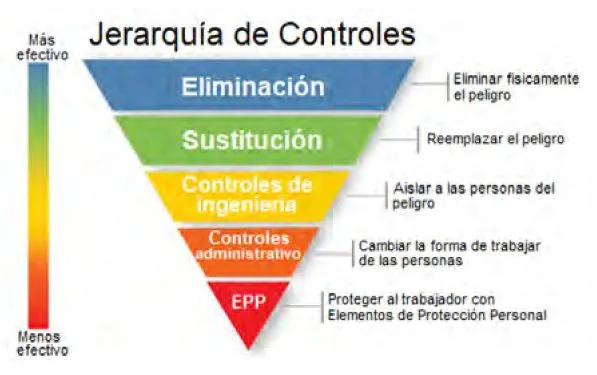
Eliminación
Dentro de la jerarquía de controles, la primera etapa en el control de riesgos que se debe priorizar es la “Eliminación”, la cual consiste básicamente en remover los peligros de los sitios de trabajo o en los procesos de la compañía, suprimiendo por completo las causas que pueden ocasionar un accidente o una enfermedad a los trabajadores. Teniendo en cuenta lo anterior, la eliminación de los peligros se puede realizar mediante el rediseño de los procesos químicos, la exclusión de sustancias químicas que sean innecesarias para el desarrollo de las actividades o en áreas en las cuales no estén directamente relacionadas con el producto final, la sustitución de equipos o máquinas por tecnología que evite la formación de contaminantes, entre otros. Con el propósito de ejemplificar este tipo de control se presentan algunos casos en la Tabla 1.
Tabla 1. Ejemplos control por eliminación.
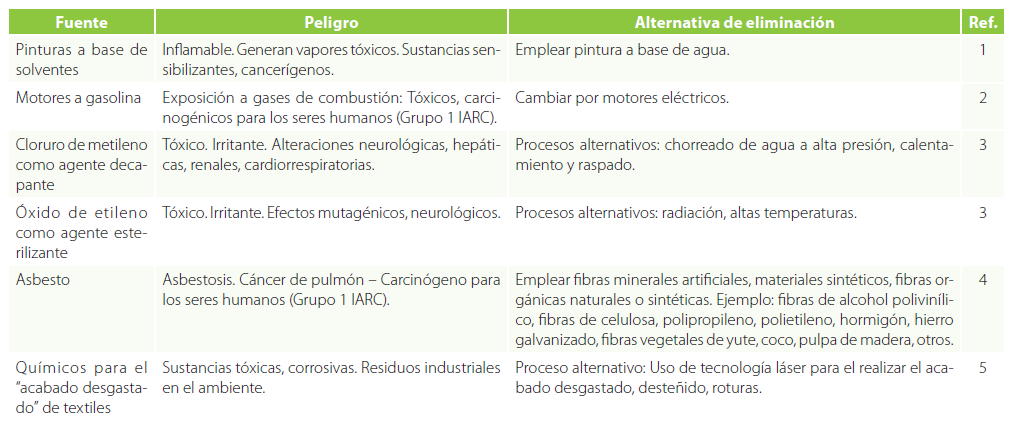
Fuente: (1) Work safe New Zealand. (2017). Identifying, assessing and managing work risk. (July), 26. (2) Departamento de Relaciones Industriales – Estado de California. (n.d.). Commission on Health and Safety and Workers’ Compensation – Home Page. https://www.dir.ca.gov/chswc/WOSHTEP/iipp/ (3) Oleart Comellas, P., Pou Serra, R., Rabassó Campi, J., & Sanz Gallén, P. (2011). Sustitución de agentes químicos. 150. (4) Takahashi, K., & Landrigan, P. J. (2016). The Global Health Dimensions of Asbestos and Asbestos-Related Diseases. Annals of Global Health, 82(1), 209–213. https://doi.org/10.1016/j.aogh.2016.01.019 (5) Green Screen. (2018). Levi’s utilizará láser para el acabado desgastado de sus pantalones. Retrieved January 9, 2020, from ttps://www.greenscreen.media/levis-laser/.
Ciertamente, aunque la estrategia de eliminación es el control que tiene la mayor efectividad en la gestión de riesgos, su implementación en procesos que se encuentren en operación requiere la modificación o actualización de dichos procesos, lo que implica adoptar nuevas tecnologías con mayor grado de complejidad, realizar inversión para la adquisición de nuevas materias primas y equipos, entre otros; motivo por el cual se recomienda realizar la eliminación de los peligros durante la etapa de planeación o diseño del proceso y de las instalaciones, dado que se remueve el peligro antes de que exista la exposición y se evita incurrir en otros gastos (“CDC – Hierarchy of Controls – NIOSH Workplace Safety and Health Topic,” 2015).
Por otro lado, cuando se habla de jerarquía de controles en la exposición a químicos, la eliminación puede no ser factible para el control de todos los peligros o suele ser una etapa compleja dado que en la mayoría de los procesos es indispensable emplear dicha sustancia debido a sus características específicas o a su aporte tanto al proceso como al producto terminado. No obstante, si dentro de los procesos se manejan o se producen sustancias que sean altamente tóxicas que estén catalogadas como cancerígenas o que sean persistentes en el ambiente, es indispensable buscar todas las alternativas posibles para realizar la eliminación de estos peligros, con el fin de garantizar la seguridad y la salud de
Sustitución
El segundo nivel de jerarquía dentro de los controles duros es la “Sustitución” de los productos químicos, y tiene por objetivo reemplazar los peligros que presenta una sustancia por una alternativa que los mitigue o que presente otros catalogados como menos severos; de igual manera, dentro de la sustitución se presentan cambios en el proceso, los cuales generan una disminución de los riesgos asociados a los peligros (Work safe New Zealand, 2017). Al igual que en el control de eliminación, se sugiere realizar la implementación del control por sustitución durante las primeras etapas de los procesos, para que no se presenten cambios drásticos a lo largo del desarrollo o funcionamiento del proceso, y de igual forma, se puedan estudiar todas las alternativas posibles a profundidad antes de efectuar el cambio (McCormick, 2019). A continuación, en la tabla 2 se relacionan algunos casos en los cuales se ha aplicado la sustitución.
Tabla 2. Ejemplos control por sustitución.
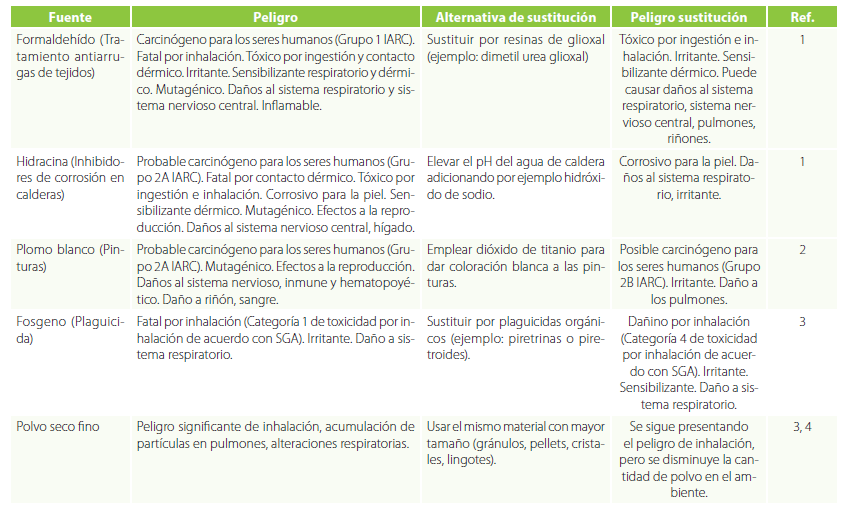
Fuente: (1) Oleart Comellas, P., Pou Serra, R., Rabassó Campi, J., & Sanz Gallén, P. (2011). Sustitución de agentes químicos. 150. (2) Buckley, R. (2010). 6 Steps to Risk Management. Worksafe ACT, (August). https://doi.org/10.1016/b978-1-85617-834-1.10004-3 (3) Canadian Centre for Occupational Health and Safety. (2018). Hazard Control: OSH Answers. from https://www.ccohs.ca/oshanswers/hsprograms/hazard_control.html. (4) Departamento de Relaciones Industriales – Estado de California. (n.d.). Commission on Health and Safety and Workers’ Compensation – Home Page. https://www.dir.ca.gov/chswc/WOSHTEP/iipp/.
Indudablemente, en la medida en que se establece la sustitución de los peligros, se observa que las alternativas encontradas introducen al proceso nuevos peligros o no se hace control completo del peligro, por lo que se debe realizar el tratamiento y manejo de los riesgos emergentes. Así mismo, cuando se hace la sustitución se debe tener en cuenta que, aunque el nuevo químico a emplear puede disminuir un peligro especifico, este al mismo tiempo puede introducir otros peligros con mayor severidad, como es el caso del amoniaco en procesos frigoríficos el cual por su toxicidad y corrosividad se sustituyó por compuestos clorofluorocarbonos que aunque tienen menor toxicidad para los seres humanos, presentan un alto impacto sobre el medio ambiente dado su potencial de destruir la capa de ozono (Oleart Comellas, Pou Serra, Rabassó Campi, & Sanz Gallén, 2011). De esta manera, la efectividad de la sustitución depende en gran medida de la decisión que se tome como sustituto, dado que se debe velar porque la opción seleccionada sea una solución más segura que la inicial.
Teniendo en cuenta lo anterior, se han establecido diferentes guías que exponen de forma clara procedimientos para abordar la sustitución de los productos químicos. Por ejemplo, la Agencia Ejecutiva para la Salud y Seguridad del Reino Unido (HSE) ha definido 7 pasos para la toma de decisiones en la planeación de esta etapa, definidos de la siguiente forma: decidir si la sustancia o el proceso son un peligro, identificar las alternativas, analizar qué puede pasar si usa las alternativas, comparar las alternativas entre ellas y con la sustancia o el proceso actual, decidir por la sustitución, introducir el sustituto y evaluar el resultado de la sustitución (Oleart Comellas et al., 2011, p. 25).
Controles de ingeniería
Cuando no se puede realizar la eliminación o sustitución de los peligros, se requiere la implementación de controles que permitan disminuir los riesgos, en efecto, la primera opción para esta medida son los controles de ingeniería, que están enfocados hacia la protección colectiva del personal y los cuales pretenden mantener alejados los riesgos de los trabajadores o evitar que los peligros tengan contacto directo con las personas; de modo que con los controles de ingeniería se busca realizar un control directo de la fuente que genera el peligro y requiere del rediseño de los procesos o equipos, de la instalación de equipos adicionales o de la organización del trabajo (EMC Insurance Companies, 2013). Para este fin, se tienen diferentes alternativas las cuales varían según diversos factores como el tipo de peligros en la empresa, el nivel de tecnificación del proceso, la disponibilidad de recursos para realizar los controles, entre otros. Dentro de los principales controles de ingeniería se presentan las siguientes posibilidades:
Aislamiento: para el manejo de sustancias químicas, el aislamiento de los peligros se puede realizar ubicando el proceso peligroso en un lugar geográficamente lejano de los trabajadores. Por otro lado, este control se tiene al encerrar el proceso a través de la implementación de barreras físicas para separar por completo a las personas de los peligros, es decir, contener las sustancias en equipos cerrados herméticamente para evitar fugas.
Automatización: corresponde a la implementación de sistemas y tecnologías que de forma independiente se encargan de hacer la operación de los equipos o la manipulación de las sustancias, evitando que sean personas las que realicen las actividades con las sustancias químicas. Dentro de esta alternativa se cuenta con ejemplos como brazos mecánicos, bandas transportadoras, dispositivos a control remoto, válvulas automáticas, entre otros.
Control de procesos: hace referencia a realizar cambios en la forma en que se desarrolla una actividad con el objetivo de disminuir los riesgos. Algunos casos de control de procesos son: usar métodos húmedos para reducir los niveles de polvo seco en el ambiente, emplear esferas de flotación en tanques que almacenan solventes para evitar la pérdida del solvente por evaporación, disminuir la temperatura de un proceso para generar menos vapores.
Ventilación: por medio de esta técnica se pretende remover o diluir los contaminantes del aire, tales como polvo, gases, humos. Este tipo de control no solo está enfocado a realizar el tratamiento de la fuente, sino que también busca hacer la remoción del peligro en el ambiente antes de que llegue a los trabajadores; debido a que se emplea principalmente la ventilación por extracción local para tratar la
fuente y la ventilación general forzada para eliminar contaminantes en el ambiente.
Otros controles que pueden tenerse a nivel industrial para evitar la exposición a químicos son: separación de materiales incompatibles, instalación de cubetas o compartimientos de retención en caso de derrames, implementación de sistemas de detección de fugas, sistemas de apagado, sistemas de alarma, equipos a prueba de explosión, eliminación de fuentes de ignición (chispas, llamas) para sustancias inflamables, etc.
En definitiva, los controles de ingeniería son una herramienta que permiten disminuir el riesgo proporcionando un alto nivel de protección, sin tener que afectar la interacción del trabajador en el proceso o de recordarle constantemente los peligros y la necesidad de protegerse. Aun cuando este tipo de control suele tener un alto costo de inversión comparado con los controles blandos, los costos operacionales que se presentan a largo término son menores que para otras alternativas (“CDC Hierarchy of Controls – NIOSHn Workplace Safety and Health Topic,” 2015). Finalmente, los controles de ingeniería deben ser diseñados, usados y contar con un mantenimiento adecuado para garantizar la efectividad del control, debido que puede llegar a presentarse el caso de que el control implementado no esté realizando su función correcta y se trabaje bajo una falsa sensación de seguridad.
Controles administrativos
En lo concerniente a los controles blandos, como primera medida se presentan los “controles administrativos”, los cuales tienen como
funcionalidad la reducción de los riesgos por medio de la limitación o la diminución de la exposición de los trabajadores al peligro, cambiar la forma como se desarrollan las actividades para asegurar que exista un trabajo seguro y minimizar la posibilidad de un mal
funcionamiento de los equipos o de los procesos. De acuerdo con la jerarquía de controles, este tipo de medidas no presenta una alta
efectividad para realizar el control de los peligros y riesgos dado que el peligro persiste en el proceso o en el ambiente, sin embargo, estas estrategias permiten reforzar los controles anteriores si se emplean en conjunto, debido a que advierten a los trabajadores sobre los peligros y las medidas necesarias para mitigar el riesgo. Los controles administrativos se pueden distinguir de acuerdo con la acción a implementar, y en estos se pueden encontrar (“CDC – Hierarchy of Controls – NIOSH Workplace Safety and Health Topic,” 2015):
◥ Prácticas de trabajo: corresponde a todas las prácticas seguras para realizar los trabajos, las cuales deben estar establecidas por
medio de procedimientos documentados y estandarizados, con instrucciones apropiadas según las funciones y los peligros potenciales, y que sean divulgadas dentro de la empresa.
◥ Organización de personal: realizar rotación del personal de una situación peligrosa a otra no peligrosa, establecimiento de horarios,
aumentar el número de descansos, asignar suficientes personas en tareas específicas como el caso de trabajo en espacios confinados, restringir el acceso al personal innecesario, permisos de trabajo para personal capacitado, agendar ciertos trabajos como el mantenimiento de equipos cuando esté presente el mínimo número de personas posible, entre otros.
◥ Señalización y etiquetado: instalación de señales, carteles, letreros de advertencia, señalización de áreas peligrosas, señales fotoluminiscentes, etiquetado correspondiente de cada sustancia química de acuerdo con normatividad vigente (ejemplo: Sistema Globalmente Armonizado).
◥ Educación y entrenamiento: hace referencia a la capacitación del personal, brindando información sobre los peligros y riesgos, entrenando sobre la forma correcta de realizar las funciones, dando herramientas para que los trabajadores pueden reconocer y evaluar
los peligros y estableciendo las medidas de protección necesarias.
◥ Prácticas de higiene personal: tiene como objetivo evitar que las sustancias químicas se absorban por la piel o sean inhaladas o ingeridas por las personas. Entre estas prácticas se encuentran: lavarse las manos después de manejar el material y antes de comer, beber y fumar, lavar rutinariamente la ropa de trabajo, evitar el contacto con la piel y los ojos, evitar la inhalación de vapores, prohibir comer o fumar en el área de trabajo.
◥ Prácticas de mantenimiento: realizar la supervisión de los riesgos, monitorización de condiciones de trabajo y condiciones ambientales, inspección y mantenimiento de equipos, procedimientos de verificaciones antes y durante el proceso, organización y
limpieza de las áreas de trabajo.
◥ Plan de prevención y preparación ante emergencias: corresponde a la adecuada preparación para el abordaje de las emergencias
presentadas, por lo que es necesario la implementación de planes adecuados sobre la atención de emergencias, procedimiento de evacuación, disponibilidad de recursos y personal, establecimiento de simulacros, entre otros.
Los principales inconvenientes que tienen estos tipos de controles son la probabilidad de que se presenten errores humanos en casos como el desarrollo de una actividad o en la inspección de un equipo, y no siempre a priori se tiene evidencia de que con la puesta en marcha de estas controles exista una reducción de la exposición de los trabajadores al riesgo (McCormick, 2019); otro inconveniente es que en la mayoría de los casos los trabajadores hacen caso omiso a las señalizaciones y las advertencias o realizan las actividades de otra forma para emplear menor tiempo o menor esfuerzo. Por otro lado, como se mencionó anteriormente, los controles administrativos son una alternativa la cual a corto plazo requiere de una pequeña inversión, sin embargo, que este tipo de control se mantenga a través del tiempo implica un alto costo para la organización (Buckley, 2010).
Elementos de Protección Personal (EPP)
La última etapa en la jerarquía de controles son los Elementos de Protección Personal (EPP), los cuales deben implementarse después
de investigar y aplicar cada uno de los controles anteriores si el riesgo persiste en el ambiente o en los lugares de trabajo, debido
a que en este nivel se delega a los trabajadores la responsabilidad en la prevención de accidentes y enfermedades (Schulte, Geraci, Zumwalde, Hoover, & Kuempe, 2008). Por consiguiente, este tipo de control se encarga de realizar la protección directa en las personas, evitando el contacto con los productos y generando una barrera entre el trabajador y la sustancia química; de modo que los elementos de protección personal deben ser utilizados por cada uno de los empleados que estén expuestos al riesgo y generalmente se usan de forma externa sobre el cuerpo. En efecto, los elementos de protección personal se encargan de brindar protección en cada una de las posibles vías de ingreso o de contacto que cada producto pueda tener en el individuo, lo que conlleva a que existan diferentes alternativas para la selección de los EPP según el tipo de sustancia y el tipo de exposición. A continuación, se presentan los principales elementos de protección personal para la exposición a productos químicos:
◥ Protección ocular: está directamente enfocada a proteger los ojos de agentes externos, dentro de los cuales se tienen partículas de polvo, humos o partículas de metales, así como salpicaduras de sustancias liquidas, o contacto con vapores que puedan producir
irritación o generar lesiones oculares. El elemento de protección fundamental en este caso son las gafas de seguridad.
◥ Protección facial: se emplean cuando se requiere un mayor grado de protección para la exposición a polvos, humos, gases y salpicadura de líquidos, dado que proporciona protección tanto de los ojos como del resto de- la cara. Una de las aplicaciones de este tipo de protección es cuando se está expuesto a gases o vapores que sean corrosivos.
◥ Protección corporal: tiene como función realizar una protección adecuada del cuerpo en general, brindando la vestimenta necesaria
para los trabajadores, cumpliendo requisitos como resistencia química, durabilidad, flexibilidad, impermeabilidad, entre otros. Dentro de la protección corporal se tienen overoles, batas, delantales, zapatos o botas de seguridad, trajes especiales.
◥ Protección manual: proporciona protección específica para las manos de los trabajadores y debe cumplir los mismos requisitos
que la protección corporal, no obstante, se deben tener en cuenta para este caso aspectos como el tiempo de contacto y la posibilidad de que exista inmersión de la mano, lo cual puede variar en el tipo de material, el grosor de los elementos, el tiempo de uso.
◥ Protección respiratoria: enfocada a realizar la protección de las vías respiratorias y depende del tipo de ambiente donde se va a
emplear y los contaminantes que este tenga, tales como polvo, humos, nieblas, gases, vapores. La protección respiratoria puede ser autónoma cuando la concentración de oxígeno no sea la adecuada o por medio de filtros según el tipo de sustancia.
En cualquier caso, la efectividad de los elementos de protección depende por un lado de la selección correcta del elemento según el tipo de peligro al cual se dé la exposición, y por el otro lado, que los EPP se ajusten adecuadamente al trabajador y este lo use según las indicaciones (Departamento de Relaciones Industriales – Estado de California, n.d.). Por tal motivo, se debe proporcionar la capacitación y entrenamiento suficiente sobre las instrucciones del uso correcto, realizar el respectivo mantenimiento y cambio de cada uno de los elementos según su vida útil, e implementar una cultura de autocuidado para que los trabajadores usen estos elementos.
Retos en la jerarquía de controles
El principal reto en la jerarquía de controles es la correcta implementación y el compromiso de las directrices en cada empresa para el
control de los riesgos, debido a que una vez identificados los peligros y evaluados los riesgos de los trabajadores, la primera acción que
suelen tomar las empresas es adoptar medidas sencillas y rápidas como lo es proporcionar elementos de protección personal o brindar capacitaciones a los trabajadores; sin embargo, se debe investigar cada uno de las cinco aspectos de forma sucesiva para identificar las alternativas más convenientes en la reducción de riesgos y tomar las medidas de control de acuerdo con la jerarquía, apuntando en la medida de lo posible al eslabón más alto de la pirámide.
Figura 3. Reto en la jerarquía de controles. Fuente: Jerarquía de Controles. (n.d.). Retrieved January 9, 2020, rom https://www.codelco.com/jerarquia-de-controles/prontus_codelco/2011-07-13/122010.html

Desde otro punto de vista, uno de los retos fundamentales para la jerarquía de controles es involucrar a los trabajadores en la etapa de
planeación de los controles, puesto que son ellos quienes están directamente expuestos a los productos químicos y a los riesgos que
estos generan, por lo que conocen las problemáticas que se originan, pueden tener conocimiento de cómo realizar el respectivo control en la gestión de riesgos, o pueden establecer si los controles son factibles y efectivos (Occupational Safety and Health Administration OSHA, n.d.).
Finalmente, esta metodología es flexible en el momento de su implementación, lo que permite que dentro del control de un mismo riesgo se puedan combinar uno o más eslabones definidos por la jerarquía de controles, considerando los beneficios para la reducción del riesgo, los costos que genera su implementación, la factibilidad y fiabilidad dentro de la operación del proceso; por lo que el reto está en saber cómo hacer la combinación de controles según las necesidades y las capacidades de la empresa. Por ejemplo, en una empresa que emplee en sus procesos una sustancia catalogada por el Sistema Globalmente Armonizado (SGA) como tóxico por inhalación categoría 1, la empresa puede buscar una materia prima sustituta la cual esté clasificada en una categoría menos severa en esta clase de peligro intrínseco, así mismo, dentro de los lugares de trabajo se deben adecuar las instalaciones para proporcionar una ventilación tanto general como localizada para asegurar que la concentración de la sustancia se mantenga lo más baja posible y que no exceda los límites de exposición ocupacional, y por último, suministrar a los trabajadores elementos de protección respiratoria con el tipo de filtro correspondiente.
Referencias
◥ Buckley, R. (2010). 6 Steps to Risk Management. Worksafe ACT, (August). https://doi.org/10.1016/b978-1-85617-834-1.10004-3
◥ Canadian Centre for Occupational Health and Safety. (2018). Hazard Control : OSH Answers. Retrieved January 8, 2020, from https://www.ccohs.ca/oshanswers/hsprograms/hazard_control.html
◥ CDC – Hierarchy of Controls – NIOSH Workplace Safety and Health Topic. (2015). Retrieved January 8, 2020, from https://www.cdc.gov/niosh/topics/hierarchy/default.html
◥ Controlling risks – WorkSafeBC. (n.d.). Retrieved January 7, 2020, from https://www.worksafebc.com/en/health-safety/create-manage/
managing-risk/controlling-risks
◥ Departamento de Relaciones Industriales – Estado de California. (n.d.). Commission on Health and Safety and Workers’ Compensation Home Page. Retrieved January 9, 2020, from https://www.dir.ca.gov/chswc/WOSHTEP/ iipp/
◥ EMC Insurance Companies. (2013). Hierarchy of Hazard Control. Retrieved January 7, 2020, from http://www.emcins.com/Docs/Risk/TechSheets/Tech_Hierarchy_Of_Hazard_Control_20130807.pdf
◥ Liberati, E. G., Peerally, M. F., & Dixon-Woods, M. (2018). Learning from high risk industries may not be straightforward: A qualitative study of the hierarchy of risk controls approach in healthcare. International Journal for Quality in Health Care, 30(1), 39–43. https://doi.
org/10.1093/intqhc/mzx163
◥ Martín Penella, M. Á. (2014). Riesgos específicos y su prevención en el sector correspondiente a la actividad de la empresa. Manual
Básico de Seguridad y Salud En El Trabajo. Retrieved from https://www.aepsal.com/wpcontent/uploads/2015/02/MB-madera_INVASSAT.
pdf
◥ McCormick, V. (2019). NIOSH’s Hierarchy of Controls – NES. Retrieved January 10, 2020, from https://www.nesglobal.net/nioshs-hierarchy-of-controls/
◥ MINISTERIO DEL TRABAJO. Decreto Numero 1072 de 2015. , Ministerio del Trabajo § (2017).
◥ Occupational Safety and Health Administration OSHA. (n.d.). Hazard Prevention and Control. Retrieved January 10, 2020, from
https://www.osha.gov/shpguidelines/hazardprevention. html
◥ Oleart Comellas, P., Pou Serra, R., Rabassó Campi, J., & Sanz Gallén, P. (2011). Sustitución de agentes químicos. 150.
◥ Organización internacional del trabajo. (2014). La seguridad y la salud en el uso de productos químicos en el trabajo. Revista, 1, 1–30.
◥ Schulte, P., Geraci, C., Zumwalde, R., Hoover, M., & Kuempe, E. (2008). Occupational risk management of engineered nanoparticles.
Journal of Occupational and Environmental Hygiene, 5(4), 239–249. https://doi.org/10.1080/15459620801907840
◥ Work safe New Zealand. (2017). Identifying, assesing and managing work risk. (July), 26.